
Meaning that each weight in the stack must support all weights below it Weight stack design is described as chain-loading or serial-loading, The assembly is raised, each weight is picked up in turn by the weightĪbove it until the transducer is loaded with the desired force. Loading frame, transducer, and yoke assembly to load the transducer. This design, a force transducer is placed between a lifting frame and a 1, which specifically depicts the 4.45 MN DWM. The design and operation of the three larger capacity DWMs is Of weights provide a large number of available mass values. Number of different force values, as the various possible combinations Measurements may thus be made for a large Operator can choose which weights to load onto the shaft andĬonsequently, the transducer. Pneumatic actuators, are lowered onto the shaft. Individual weights, which are otherwise held up by hydraulic or

Smaller-capacity DWMs, the transducer is loaded by a main shaft, and

Two different operational designs of DWMs at NIST. Individual stainless steel weights (1) to the supported load. Which has disseminated force units to a worldwide customer base.ġ.1 Operation and History of the Deadweight MachinesĬalibrations of force transducers are performed by applying aĭiscrete set of applied forces to the transducer by the addition of International resource for SI-traceable measurements of large forces Metrology institutes across the world thus, the 4.45 MN DWM is an It was the centerpiece of two International KeyĬomparisons of primary large force measurements at several national With each calibration typically involving several applications of theįull 4.45 MN force. Is presently the largest deadweight force standard in the world, and hasīeen used to perform thousands of force transducer calibrations to date, To provide force calibrations to industry, government labs, and academiaįor numerous applications including for example space programs. Starting from its first years of operation, this machine has been used Over 25 m and has been in use in the NIST Force Laboratory since 1965. The largest DWM is the 4.45 MN apparatus, which has a height of Transducer-dependent, but expanded uncertainties (k = 2) can be as small The calibration uncertainty achieved using these machines is In these machines, theįorce applied to a transducer is generated by Earth's gravityĪcting on a calibrated mass, which may be written F = mg where m is massĪnd g is Earth's gravitational acceleration, wherein the mass hasīeen corrected for buoyancy effects of the local atmosphere. Located on the NIST Gaithersburg, MD campus. Special building with strictly controlled environmental conditions These six machines have maximum force capacities of 2.25 kN

(load cells), which output a voltage when a force is applied to the Typically, theseĭeadweight machines are used to calibrate elastic force transducers
#Nist comsol 5.3 series#
Series of six deadweight force machines (DWMs). The National Institute of Standards and Technology (NIST) Mass andįorce Group provides SItraceable force calibration services ranging fromĤ4 N to 4.448 MN based on primary deadweight force standards using a
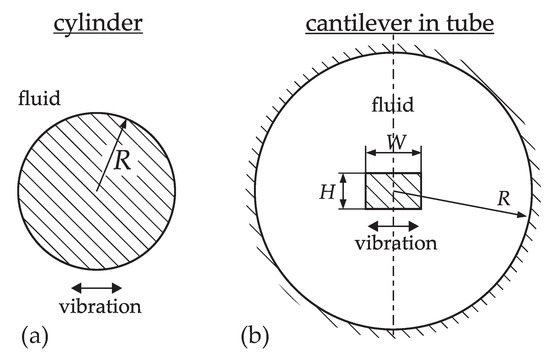
#Nist comsol 5.3 free#
MLA style: "Stress Analysis of Conical Contact Joints in the NIST 4.45 MN Deadweight Machine." The Free Library.
